Refractory Materials for Induction Furnace Lining
- social9778
- Aug 7, 2024
- 4 min read
Induction furnaces are widely used. The design of large medium-frequency crucible induction furnaces often requires consideration of refractory materials for the furnace lining. Induction furnace lining refractory materials. In general, the lining materials of induction furnaces are based on the utilization rate and economy of the furnace.
Requirements for refractory materials of induction furnace lining
In order to ensure the normal operation of the induction furnace, the refractory materials of the furnace lining generally have the following requirements.
1. Sufficient refractoriness.
Materials with a refractoriness higher than 1580℃ are called refractories. The working temperature of the furnace lining is generally lower than the temperature of the molten metal. However, based on the requirements for the life of the furnace lining, it is also necessary to consider that the temperature in some areas of the furnace body is too high. In cast iron induction furnaces, it is often unsafe to use materials with low refractoriness. As the lining material of the cast iron induction furnace, its refractoriness should be greater than 1650-1700℃.
2. Good thermal stability.
The induction furnace relies on electromagnetic induction to exchange and transfer energy. In order to ensure that the electric furnace has a higher electrical efficiency, the thickness of the lining of the induction coil part is limited. In addition, the temperature of the furnace lining is always changing due to the influence of charging, tapping and even stopping the furnace during the operation of the furnace. The furnace lining often cracks due to uneven heating, which reduces the service life of the furnace lining. Therefore, as a refractory material for an induction furnace, it should have excellent thermal stability.
3. Good chemical stability.
The chemical stability of the material is closely related to the life of the furnace lining. At low temperatures, the furnace lining material must not be hydrolyzed and differentiated. At high temperatures, it is not easy to decompose and reduce. During the smelting process, the furnace lining material is not easy to form a low-melting-point substance with the slag, and will not react chemically with the solution and additives.
4. Small thermal expansion coefficient. As the temperature changes, the volume should be relatively stable, without drastic expansion and contraction.
5. It has high mechanical properties. It must be able to withstand the impact of the charge at low temperatures. When the metal is in a high-temperature molten state, it should be able to withstand the pressure of the molten metal and the strong electromagnetic stirring. It is wear-resistant and corrosion-resistant under the long-term scouring of the metal.
6. Good insulation performance. The furnace lining must not be conductive at high temperatures, otherwise it will cause leakage and short circuits, causing serious accidents.
7. The material has good construction performance. It should be easy to repair and sinter, and convenient to build and repair the furnace.
The requirements for refractory materials in induction furnaces are still quite strict. This requires us to select appropriate refractory materials according to different usage requirements so that their performance can meet the various requirements of the induction furnace.
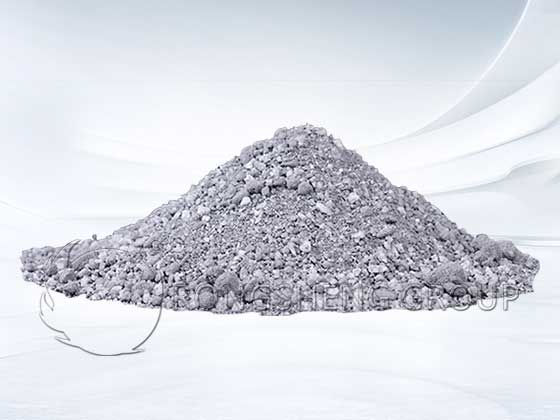
Refractory materials for copper and copper alloy induction furnaces
At present, the lining systems commonly used in copper and copper alloy coreless induction furnaces are mainly corundum and quartz dry ramming materials. There are also preformed graphite crucibles and silicon carbide crucibles, and the backing of the crucible is a non-sintered filler. Quartz ramming material has low cost and is easy to build a furnace. It can be used for up to 200 furnaces in a 300~700kg furnace. When the working temperature is increased and the working environment is more demanding, the corundum lining shows its superiority and has a longer service life. However, the cost of the material is 7~8 times higher than that of quartz.
The outstanding advantage of pre-synthesized clay combined with graphite crucible and silicon carbide crucible is that it can be replaced quickly and saves sintering time. At the same time, the use of graphite as a binder can increase the conductivity of the crucible, thereby improving the electrical efficiency of the induction furnace, and the temperature in the crucible is naturally high. However, the heat loss of this lining is large and the energy saving effect is poor. Its advantages of easy replacement, no sintering and energy saving benefits may not compensate for the cost difference between the formed crucible and the corundum lining. At the same time, the stirring effect in the crucible is reduced, which is not conducive to the uniformity of the furnace temperature. In addition, in large coreless furnaces that are used continuously, mullite or high-alumina ramming materials and castables similar to cored linings can be used. The above materials have a long furnace building and baking cycle and require continuous use. The general service life can reach more than one year.
For high-quality refractory lining materials for induction furnaces and refractory materials for copper alloy induction furnaces, please choose Rongsheng Refractory Material Manufacturers. We provide high-quality refractory lining materials and comprehensive customer service. Contact us for free samples and quotes.
Comments