Lightweight Mullite Insulation Castable Ladle Permanent Layer Insulation
- social9778
- Jan 16, 2024
- 4 min read
Ladle is an essential container in the steelmaking process. With the continuous development of smelting technology, especially the processing of out-of-furnace refining LF and RH, the role of the ladle has evolved from the simplest collection of molten steel to a furnace that undertakes certain smelting functions. If the molten steel stays in the ladle for a long time, the temperature of the molten steel will inevitably be lost, and the ladle lining with high thermal conductivity will increase the heat loss of the molten steel. The deformation of the ladle shell becomes more serious, and the temperature of the molten steel decreases at an increased rate. This results in serious slag hanging, nodules, and cold steel on the wall of the package. Excessive low temperature may even force the middle package to cut off the flow and final pouring. It not only affects the quality of the cast slab, but also reduces the molten steel yield and increases the production cost.

Configuration of Refractory Materials for Ladle Insulation Layer
Therefore, thermal insulation ladles are increasingly becoming a requirement for steel mills. The refractory structure mode of thermal insulation ladle is usually lightweight insulation board or nano board + permanent layer castable + working layer refractory material. Lightweight mullite refractory castable has excellent high temperature performance, small volume density and thermal conductivity. Because it uses synthetic raw materials, it is combined with low cement or micro powder. So it acts as a kiln lining that has direct contact with the flame.
The insulation board, which plays the most important role in thermal insulation, needs a layer of refractory material to protect it. This kind of material should firstly protect the thermal insulation material from too much pressure, and secondly, protect the thermal insulation material from exceeding the operating temperature (for example, it must be below 1000°C). Then the castable for the permanent layer of the ladle is this important material. The ideal permanent layer refractory material for thermal insulation ladle should have good thermal stability, heat preservation and corrosion resistance. It has the characteristics of safe and reliable application, complete structure and long service life. In order to maintain good thermal insulation performance of the ladle and reduce the temperature drop of the molten steel, lightweight mullite castables were applied and performance evaluated on the ladle, achieving a relatively good comprehensive thermal insulation effect.
Insulated ladles have become an important technical measure for steel companies to save energy, protect the environment, and improve the quality of steel products. The permanent layer materials of ladles have been given higher requirements. The physical properties of the lightweight mullite insulation castable and the strength and other physical properties of the lightweight mullite castable meet the application requirements of the permanent layer of the ladle. At the same time, it has better thermal insulation and corrosion resistance than conventional high-aluminum castables, and can protect thermal insulation materials. To maintain good thermal insulation of the ladle during the furnace service period. Further in-depth research is needed on the comprehensive technology to reduce the cracking of the permanent layer material of the thermal insulation ladle.
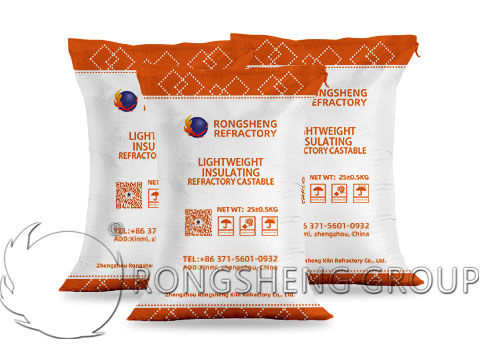
Characteristics of Thermal Insulation Castables
Characteristics of lightweight thermal insulation castables and refractory thermal insulation castables. Refractory castables, as the main type of monolithic refractory materials, have the common feature of being used directly without firing. The production process is relatively simple among many types of monomorphic refractory materials. Refractory material manufacturer does not require special equipment, has a high degree of mechanization, simple construction and high material utilization rate. In addition, it generally has high normal temperature strength and can be made into prefabricated parts and installed at the kiln turning site.
Performance and Advantages of Thermal Insulation Refractory Castables
Thermal insulation refractory castables are composed of high-strength materials as aggregates and fine powder composite additives. It has the advantages of high refractoriness, high strength and low thermal conductivity. Insulating refractory castables have the characteristics of small volume density and low thermal conductivity. This can reduce the heat consumption of industrial kilns. At the same time, the weight of the furnace lining can also be reduced.
Refractory insulation castables are mainly used for the insulation layer of kilns and are refractory materials for kiln heat resistance. It has good thermal insulation effect and is the energy-saving material of choice for kilns. Medium-quality thermal insulation castables have small volume density, large porosity and small heat transfer coefficient, which can effectively prevent the loss of heat from the furnace wall. Save energy, improve fuel utilization, save energy and protect the environment.
Refractory and thermal insulation castables are mainly used in metallurgical industrial kilns. It is also widely used in furnaces and thermal equipment in the petroleum, chemical, building materials, electric power and machinery industries.
Refractory insulation castable is a granular and powdery material made of refractory substances, and is composed of a certain amount of binder and moisture. It has high fluidity, is suitable for construction by pouring method, and is an unshaped refractory material that can be hardened without heating.
Comments